فیلرها در تولید کاشی و سرامیک
ز نظر ساخت چند نوع سرامیک داریم؟
سرامیک ها به طور کلی به چهار دسته زیر تقسیم می شوند:
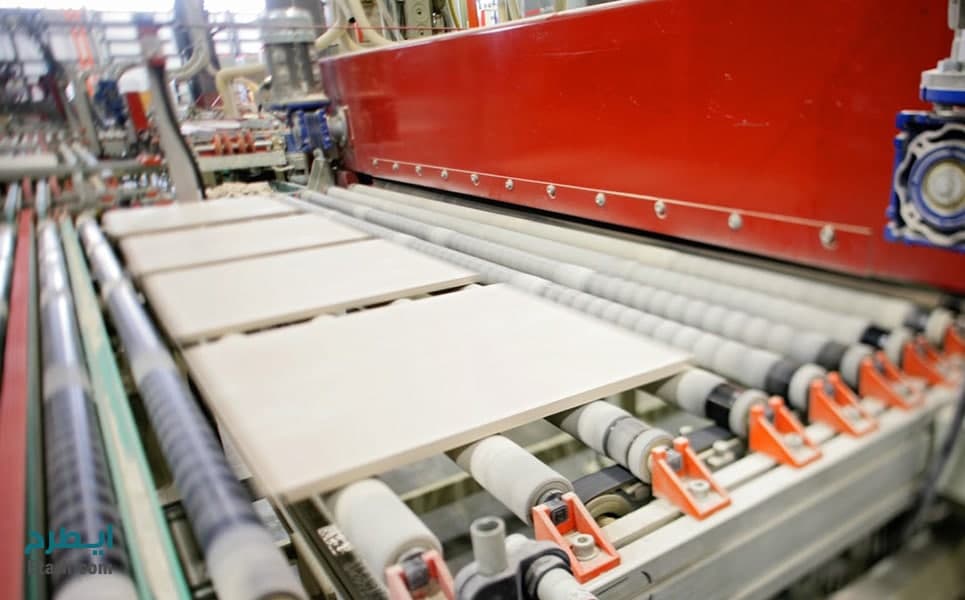
فراورده های سرامیکی که در این میان بیشترین استفاده را دارند، خود در دسته بندی های زیر تقسیم می شوند.
دستگاه های مورد استفاده برای تولید سرامیک و کاشی
در کارخانه های برای تولید محصولات خود از ابزارآلات پیشرفته و کربنات کلسیم مربوط به هر مرحله استفاده می کنند؛ این دستگاه ها به ترتیب استفاده در مراحل ساخت سرامیک عبارتند از:
“سنگ شکن، باکسفیدر، بالمیلدوغاب و لعاب، اسپری درایر، دستگاه پرس، کوره های رولری و تونلی، خط لعاب و دکور زنی، دستگاه های مربوط به بسته بندی و درجه بندی”
در ادامه مراحل تولید کاشی و سرامیک را برای شما توضیح می دهیم و شما را با این روند آشنا می کنیم.
مراحل تولید سرامیک و کاشی در کارخانه ها
مرحله اول: آماده کردن مواد اولیه مورد نیاز برای ساخت کاشی و سرامیک
بدنه کاشی ها معمولا از خاک های مختلف که در شرایط مختلف و از معادن مختلف برداشت می شود. این کاشی و سرامیک ها خود بر اساس کاربرد و نقشی که دارند، از مواد اولیه متفاوتی ساخته می شوند که عبارتند از: مواد اولیه پلاستیک، پر کننده یا فیلر ها و کمک ذوب ها یا گداز آور ها.
منظور از موارد اولیه پلاستیک همان خاصیت پودر سیلیس خاک رس است که به صورت زیر تعریف می شود: خاصیت پلاستیسیته خاصیتی است که به وسیله آن یک جسم می تواند در اثر فشار و ضربه حالت ارتجاعی داشته باشد و بدون شکستن، تغییر شکل دهد و بعد از رفع فشار یا ضربه دوباره به حالت اول خود باز گردد. یکی از ویژگی های خاک رس داشتن پلاستیسیته است.
پر کننده ها یا فیلر ها به مواد غیر پلاستیک گفته می شود که دارای دما ذوب بالا و مقاومت شیمیایی بالایی می باشند و وظیفه آن ها این است که از تغییر شکل بدنه در زمان پخت و حرارت دهی جلوگیری کنند. همچنین این موارد کمک می کنند که لعاب با کیفیت بهتری با خود سرامیک پیوند برقرار کند.
گداز آور ها موادی هستند که به دلیل کاهش نقطه ذوب بدنه یا هم لعاب، مصرف بالایی در سرامیک و کاشی سازی دارند. این مواد در زمان حرارت دادن ذوب می شوند و وقتی در حال سرد شدن هستند به حالت شیشه در می آیند. مهمترین گداز آور های بدنه که برای کاشی و سرامیک مورد استفاده قرار می گیرد و مهم ترین گداز آور ها عبارتند از: اکسید های پتاسیم، سدیم، کلسیم و منیزیم که برای تامین آن ها باید از فلدسپات های سدیک، کلسیک و پتاسیک استفاده کرد.
قسمت بعدی که در مرحله اول قرار می گیرد آماده سازی این مواد اولیه است که روند این کار ها به نوع مواد و اندازه آن ها بستگی دارد که در ادامه به صورت مختصر توضیح می دهیم:
نکته ای که در این میان باید در نظر داشته باشید این است که در هر مرحله باید نظارت ها طبق استاندارد هایی انجام شود.
مرحله دوم: آماده سازی پودر
برای آماده ساختن پودر از دوغاب، باید از اسپری درایر یا همان خشک کن های افشان استفاده کرد. دوغابی که در آسیاب ها درست شده است در مخازن دوغاب ریخته می شود که این موضوع باعث یکدست شدن آن می شود، سپس پمپ هایی با فشار بالا دوغاب را به یک محفظه استوانه ای که اسپری درایر نام دارد می رسانند و آن دوغاب را در هوا اسپری می کنند، دوغاب در این محل با هوای گرم و خرارت برخورد می کند و در پایان پودری نرم روی نوار نقاله زیر این استوانه ریخته می شود. کیفیت این پودر به عواملی مانند: ” نوع نازلهای پاشنده و تعداد و انداز سوراخ و آرایش آنها، نوع اسپری درایر، کیفیت پمپاژ و فشار پمپ، رطوبت پودر و دانه بندی پودر، ابعاد محفظه، کیفیت دوغاب و فرمول بدنه و خصوصاً پلاستیسیته آنها و دانسیته و وسیکوزیته و دانه بندی دوغاب، حرارت داخل محفظه، فشار داخل محفظه و میزان رطوبت محفظه، ثبات فشار گاز، ماندگاری پودر، استحکام پودر و هموژن بودن رطوبت آنها، جنس نازلها و سایر اجزاء نازل” بستگی دارد.
مرحله سوم: شکل دهی یا پرس کردن پودر
این روش به این صورت است که مخلوط مواد اولیه که به صورت پودری با دانه بندی مناسب در آمده در حفره های قالب و تحت فشار قرار می گیرد و به این صورت شکل قالب را به خود می گیرد. در این شرایط رطوبت موجود در پودر باید حدود 5 درصد باشد. امروزه در صنایع تولید کاشی، پرس های بسیار مدرن و با توانمندی های بالا وجود دارد که حتی می توانند طرح را در مرحله پرس کردن اعمال نمایند.
مرحله چهارم: خشک کردن سرامیک و کاشی
در زمان هایی قدیم خشک کردن در تونل ها طولانی انجام میشد و این کار تا چند روز طول می کشید، این در حالی ست که اگر شما از دستگاه های خشک کن مدرن استفاده کنید می توانید بعد از حدود 20 دقیقه سرامیک های خود را خشک کنید. همچنین خشک شدن به روش قدیمی باعث بروز مشکلاتی مانند ترک خوردگی و جای گذاشتن سرامیک ها و کاشی ها روی هم میشد که این موضوع حتی بعد از لعاب کاری جلوه کار را از بین می برد. البته این مشکلات با استفاده از دستگاه ها جدید حل شده است
مرحله پنجم: انجام لعاب کاری و اصلاحات ظاهری
در کاشی های تک پخت مانند نمونه کاشی دیواری منوپروزا، کاشی های کف و پرسلان لعاب دارد بعد از خشک کاری کاشی، وارد مسیر آبی می شوند و سپس لعاب کاری آستری که به آن آنگوب نیز می گویند روی آنها اعمال می شود و سپس لعاب کاری توسط دستگاه های دیگر انجام شده و طرح های مورد نظر روی کاشی و سرامیک انجام می شود. البته گفتنی است که هر رنگ از چاپ باید توسط دستگاه مجزایی انجام شود که البته این موضوع به مواردی مانند طول خط تولید، خشک شدن کاشی و سرامیک ها بعد از هر مرحله از لعاب کاری بستگی دارد. ماشین آلات جدید که برای لعاب کاری مورد استفاده قرار می گیرند به این صورت می باشند که می توانند چاپ های بیشتری روی کاشی اعمال کنند. مراحل لعاب کاری به صورت زیر می باشد:
مرحله ششم: پخت سرامیک و کاشی مورد استفاده
بعد از این که لعاب کاری انجام شد، نوبت به پخت کاشی و سرامیک می رسد. اساس پخت کاشی منحنی زمان-دما است که به آن منحنی پخت کاشی نیز می گویند و این منحنی برای محصولات مختلف و کاشی هایی با استفاده های مختلف متفاوت است و این منحنی با توجه به دما ها و تنظیمات ترموکوپل موجود در دیواره ها یا سقف کوره در نظر گرفته می شود. بازده و راندمان پخت کاشی به به انرژی گرمایی بستگی دارد که توسط محصولاتی که در کوره قرار گرفته اند جذب می شود. در صورتی که در این مرحله توجه کافی به موضوع پخت نشود و اصول لازم برای انجام این کار رعایت نشود ممکن است که به مشکلاتی مانند مواردی که در ادامه برای شما بیان می کنیم بر بخورید:
مرحله هفتم: پولیش کاری
این مرحله فقط برای کاشی های گرانیتی بدون لعاب انجام می شود، کاشی های گرانیتی به دسته ای از کاشی ها گفته می شود که قدرت جذب آب آنها کمتر از نیم درصد باشد. زمانی که پولیش کاری انجام می شود روزنه هایی که احتمالا روی سطح وجود دارد. این روزنه ها به علاه بر این که باعث کاهش عمر کاشی و سرامیک و نفوظ آب در آن می شود.
روش بایر برای تولید پودر سرامیک
ماده ی اولیه ی مورد استفاده در روش بایر بوکسیت است. این بوکسیت باید خلوصی بیش از 55 درصد داشته باشد تا فرآیند بایر صرفه ی اقتصادی داشته باشد. ماده ی اولیه ی بدست آمده از معدن (بوکسیت) خردایش شده و در مخازن بزرگ و سربسته ی آب در سود حل می گردد. با حل شدن بوکسیت در آب و بوسیله ی سودسوزآور، در محلول آلومینات سدیم به صورت محلول در آب تشکیل می شود. در مرحله ی بعد ناخالصی های نامحلول مانند آهن، سیلیس وتیتان بوسیله ی فیلتراسیون جدا می گردند. این ناخالصی ها به لجن قرمز (redmad) معروفند. در مرحله ی بعد برای عکس کردن واکنس انحلال هیدروکسید، گاز دی اکسید کربن به داخل محلول دمیده می شود. و رسوب Al(OH)3 تشکیل می شود. رسوب حاصله جداسازی، خشک و کلسیناسیون می شود. آلومینای حاصله خردایش و دانه بندی می گردد.به آلومینای بدست آمده از روش بایر، آلومینای کلسینه شده می گویند. عمل کلسیناسیون در روش بایر در کوره ی دوار صورت می پذیرد. در ابتدای کوره دما پایین است و عمل خشک شدن انجام می شود. و در ادامه عمل تجزیه صورت می پذیرد. ترکیباتی همچون کلرین ها، فلرین ها، بور می توانند دمای تجزیه ی هیدروکسید آلومینیوم را کاهش دهند. همچنین این عوامل، عامل جوانه زا برای تشکیل α- آلومینا هستند. وعلاوه بر دمای تجزیه ی هیدروکسید، بر روی شکل ذرات نهایی اثرگذار هستند. هر چه دمای کوره (دمای تجزیه) بالاتر رود، تبدیل می تواند کامل تر صورت گیرد. در دمای 1400 درجه سانتیگراد در حدود 99-90درصد از هیدروکسید به α-آلومینا تبدیل می شود و علاوه بر α آلومینا فاز میانی ð نیز وجود دارد. از این رو برحسب دمای کوره و افزودنی های مختلف، درصد α-آلومینا متفاوت است. در روش بایر حتی می توان آلومینایی با خلوص 99.99 درصد تولید نمود.