روش های ایمن کار با آمونیاک و نکات مهم در حمل ونقل و ذخیره سازی
آمونیاک گازی بی رنگ با بوی تند و زننده به دلیل خواص شیمیایی و فیزیکی منحصر به فرد خود کاربردهای گسترده ای در صنایع مختلف از جمله کشاورزی صنایع غذایی پتروشیمی و سیستم های برودتی دارد. با این حال ماهیت سمی و خورنده آمونیاک ضرورت رعایت دقیق اصول ایمنی در کار با آن به ویژه در مراحل حمل ونقل و ذخیره سازی را اجتناب ناپذیر می سازد. این مقاله با هدف ارائه یک راهنمای جامع و تخصصی در زمینه روش های ایمن کار با آمونیاک نکات کلیدی در حمل ونقل و ذخیره سازی و بررسی استانداردها و فناوری های نوین مرتبط با این ماده خطرناک تدوین شده است.
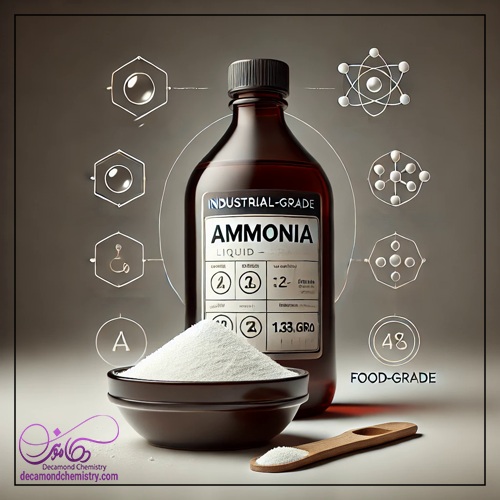
اجزای اصلی سیستم های آمونیاکی و اصول کارکرد آن ها
سیستم های آمونیاکی بسته به کاربرد می توانند بسیار متنوع باشند اما اجزای اصلی آن ها در بیشتر موارد مشابه است. درک عملکرد فنی این اجزا بر اساس اصول مهندسی کلید ایمنی و کارایی سیستم های آمونیاکی است.
مخازن ذخیره سازی آمونیاک : قلب سیستم
مخازن ذخیره سازی آمونیاک به عنوان اصلی ترین بخش سیستم وظیفه نگهداری ایمن و مطمئن آمونیاک را بر عهده دارند. این مخازن معمولاً از جنس فولاد کربنی یا فولاد آلیاژی با مقاومت بالا در برابر فشار و خوردگی ساخته می شوند. طراحی و ساخت مخازن ذخیره سازی آمونیاک مطابق با استانداردهای بین المللی مانند ASME Boiler and Pressure Vessel Code و API ۶۲۰ انجام می شود.
اصول کارکرد فنی مخازن ذخیره سازی :
- فشار طراحی : مخازن آمونیاک باید توانایی تحمل فشار داخلی ناشی از بخار آمونیاک در دماهای مختلف عملیاتی و شرایط اضطراری را داشته باشند. فشار طراحی مخزن بر اساس حداکثر فشار کاری مجاز (MAWP) و ضریب ایمنی مناسب تعیین می شود.
- عایق بندی : در برخی کاربردها مخازن آمونیاک برای کاهش تبخیر و حفظ دمای پایین آمونیاک مایع عایق بندی می شوند. عایق بندی می تواند به صورت خارجی (مانند پشم سنگ یا فوم پلی یورتان) یا داخلی (مانند عایق های پرلیت) انجام شود.
- سیستم های ایمنی : مخازن آمونیاک مجهز به سیستم های ایمنی متعددی هستند که از جمله مهم ترین آن ها می توان به موارد زیر اشاره کرد :
- شیرهای اطمینان (Pressure Relief Valves – PRVs) : این شیرها در صورت افزایش ناگهانی فشار داخلی مخزن به دلیل حرارت یا انبساط حرارتی آمونیاک به طور خودکار باز شده و با تخلیه بخشی از بخار آمونیاک فشار را به حد مجاز بازمی گردانند. ظرفیت تخلیه شیرهای اطمینان باید بر اساس محاسبات دقیق و با در نظر گرفتن بدترین سناریوهای ممکن تعیین شود.
- شیرهای قطع اضطراری (Emergency Shut-Off Valves – ESOVs) : این شیرها که معمولاً به صورت پنوماتیکی یا الکتریکی عمل می کنند در مواقع اضطراری مانند نشت آمونیاک یا آتش سوزی به سرعت جریان آمونیاک را قطع کرده و از گسترش حادثه جلوگیری می کنند.
- سیستم های اعلام و اطفاء حریق : مخازن آمونیاک در محیط های صنعتی معمولاً مجهز به سیستم های اعلام و اطفاء حریق هستند که شامل دتکتورهای گاز آمونیاک دتکتورهای حرارتی و سیستم های اطفاء حریق خودکار (مانند سیستم های آب پاش یا فوم) می باشند.
- سیستم های تهویه : محوطه اطراف مخازن آمونیاک باید دارای سیستم تهویه مناسب باشد تا در صورت نشت جزئی آمونیاک غلظت آن در هوا به حد مجاز نرسد.
خطوط لوله و اتصالات : مسیر انتقال آمونیاک
خطوط لوله و اتصالات نقش حیاتی در انتقال آمونیاک بین اجزای مختلف سیستم (مانند مخازن ذخیره سازی مبدل های حرارتی کمپرسورها و غیره) ایفا می کنند. جنس لوله ها و اتصالات معمولاً از فولاد کربنی یا فولاد ضدزنگ با توجه به فشار و دمای کاری سیستم و همچنین خورندگی آمونیاک انتخاب می شود. طراحی و نصب خطوط لوله آمونیاک باید مطابق با استانداردهای مهندسی مانند ASME B۳۱.۳ و EN ۱۳۴۸۰ انجام شود.
اصول کارکرد فنی خطوط لوله و اتصالات :
- انتخاب مواد مناسب : مواد مورد استفاده در ساخت خطوط لوله و اتصالات باید مقاومت کافی در برابر خوردگی آمونیاک فشار و دمای کاری سیستم را داشته باشند. فولاد کربنی به طور گسترده ای برای خطوط لوله آمونیاک مایع و گازی در دماهای معمولی استفاده می شود اما در دماهای پایین تر یا در محیط های خورنده فولادهای آلیاژی یا فولادهای ضدزنگ ممکن است مورد نیاز باشند.
- جوشکاری و اتصالات : اتصالات خطوط لوله آمونیاک معمولاً با استفاده از روش های جوشکاری تخصصی مانند جوشکاری قوسی با گاز محافظ (GTAW) یا جوشکاری قوسی فلزی با گاز محافظ (GMAW) انجام می شود. جوشکاران باید دارای گواهینامه های معتبر و آموزش های لازم در زمینه جوشکاری خطوط لوله آمونیاک باشند. اتصالات فلنجی و رزوه ای نیز در برخی موارد استفاده می شوند اما باید از آب بندی مناسب و استفاده از مواد آب بند سازگار با آمونیاک اطمینان حاصل شود.
- آزمایش های غیرمخرب (NDT) : پس از نصب خطوط لوله و اتصالات انجام آزمایش های غیرمخرب مانند آزمایش رادیوگرافی (RT) آزمایش ذرات مغناطیسی (MT) و آزمایش مایع نافذ (PT) برای اطمینان از کیفیت جوش ها و عدم وجود عیوب احتمالی ضروری است.
- تست فشار (Pressure Testing) : قبل از بهره برداری خطوط لوله آمونیاک باید تحت تست فشار هیدرواستاتیک یا پنوماتیک قرار گیرند تا از استحکام و آب بندی آن ها اطمینان حاصل شود. فشار تست معمولاً ۱.۵ برابر فشار طراحی سیستم در نظر گرفته می شود.
پمپ ها و کمپرسورها : جریان دهنده های آمونیاک
پمپ ها و کمپرسورها وظیفه انتقال و افزایش فشار آمونیاک در سیستم را بر عهده دارند. نوع پمپ یا کمپرسور مورد استفاده به نوع آمونیاک (مایع یا گاز) فشار و دبی مورد نیاز سیستم بستگی دارد.
اصول کارکرد فنی پمپ ها و کمپرسورها :
- پمپ های آمونیاک مایع : پمپ های آمونیاک مایع معمولاً از نوع پمپ های سانتریفیوژ یا پمپ های جابجایی مثبت (مانند پمپ های پیستونی یا پمپ های دنده ای) هستند. انتخاب نوع پمپ به دبی فشار و ویسکوزیته آمونیاک مایع بستگی دارد. پمپ های سانتریفیوژ برای دبی های بالا و فشارهای متوسط مناسب هستند در حالی که پمپ های جابجایی مثبت برای دبی های پایین و فشارهای بالا کاربرد دارند.
- کمپرسورهای آمونیاک گازی : کمپرسورهای آمونیاک گازی معمولاً از نوع کمپرسورهای رفت و برگشتی (پیستونی)کمپرسورهای اسکرو یا کمپرسورهای سانتریفیوژ هستند. کمپرسورهای پیستونی برای فشارهای بالا و دبی های پایین کمپرسورهای اسکرو برای دبی های متوسط و فشارهای متوسط و کمپرسورهای سانتریفیوژ برای دبی های بالا و فشارهای پایین تر مناسب هستند.
- آب بندی : پمپ ها و کمپرسورهای آمونیاک باید دارای آب بندی مناسب برای جلوگیری از نشت آمونیاک به محیط باشند. آب بندهای مکانیکی (Mechanical Seals) و آب بندهای مغناطیسی (Magnetic Seals) از جمله رایج ترین انواع آب بندهای مورد استفاده در پمپ ها و کمپرسورهای آمونیاک هستند.
- خنک کاری : فشرده سازی آمونیاک گاز باعث افزایش دما می شود. بنابراین کمپرسورهای آمونیاک معمولاً مجهز به سیستم های خنک کاری (مانند خنک کاری با آب یا هوا) هستند تا دمای آمونیاک را در حد مجاز نگه دارند و از آسیب به کمپرسور و سیستم برودتی جلوگیری شود.
سیستم های برودتی آمونیاکی : سرمایش صنعتی
سیستم های برودتی آمونیاکی به دلیل راندمان بالا و سازگاری با محیط زیست (در مقایسه با برخی مبردهای مصنوعی) به طور گسترده ای در صنایع مختلف مانند صنایع غذایی (سردخانه ها کارخانجات فرآوری مواد غذایی) صنایع پتروشیمی و تهویه مطبوع صنعتی مورد استفاده قرار می گیرند. آمونیاک به عنوان مبرد در این سیستم ها با جذب گرما از محیط و تبخیر باعث ایجاد سرمایش می شود.
اصول کارکرد فنی سیستم های برودتی آمونیاکی :
- سیکل تبرید تراکمی : سیستم های برودتی آمونیاکی معمولاً بر اساس سیکل تبرید تراکمی کار می کنند. این سیکل شامل چهار مرحله اصلی است :
- تراکم (Compression) : کمپرسور بخار آمونیاک کم فشار و کم دما را فشرده کرده و به بخار آمونیاک پرفشار و پردما تبدیل می کند.
- تقطیر (Condensation) : بخار آمونیاک پرفشار و پردما در کندانسور (مبدل حرارتی) با از دست دادن گرما به محیط (هوا یا آب) به آمونیاک مایع پرفشار تبدیل می شود.
- انبساط (Expansion) : آمونیاک مایع پرفشار از شیر انبساط عبور کرده و فشار آن به طور ناگهانی کاهش می یابد. این کاهش فشار باعث تبخیر بخشی از آمونیاک مایع و کاهش دمای آن می شود.
- تبخیر (Evaporation) : آمونیاک مایع کم فشار و کم دما در اواپراتور (مبدل حرارتی) با جذب گرما از محیط (فضای سردخانه یا فرآیند صنعتی) تبخیر شده و به بخار آمونیاک کم فشار و کم دما تبدیل می شود. بخار آمونیاک سپس به کمپرسور بازمی گردد و سیکل تکرار می شود.
- مبدل های حرارتی : مبدل های حرارتی (کندانسور و اواپراتور) اجزای کلیدی سیستم های برودتی آمونیاکی هستند که وظیفه انتقال حرارت بین آمونیاک و محیط را بر عهده دارند. انواع مختلفی از مبدل های حرارتی مانند مبدل های پوسته لوله (Shell and Tube Heat Exchangers) مبدل های صفحه ای (Plate Heat Exchangers) و مبدل های هوا خنک (Air-Cooled Heat Exchangers) در سیستم های برودتی آمونیاکی استفاده می شوند.
- کنترل ظرفیت : سیستم های برودتی آمونیاکی معمولاً مجهز به سیستم های کنترل ظرفیت هستند تا بتوانند با تغییر بار برودتی عملکرد سیستم را بهینه کرده و مصرف انرژی را کاهش دهند. روش های کنترل ظرفیت شامل تغییر دور کمپرسور (Variable Speed Drive – VSD) بای پس گاز داغ (Hot Gas Bypass) و خاموش و روشن کردن کمپرسور (Compressor Cycling) می باشد.
کاربردهای صنعتی آمونیاک و مثال هایی از صنایع مختلف
آمونیاک به دلیل خواص منحصر به فرد خود کاربردهای گسترده ای در صنایع مختلف دارد که برخی از مهم ترین آن ها عبارتند از :
- صنایع کشاورزی : بیشترین کاربرد آمونیاک در تولید کودهای شیمیایی نیتروژنه است. آمونیاک به صورت مستقیم یا به عنوان ماده اولیه در تولید کودهای اوره نیترات آمونیوم و سولفات آمونیوم استفاده می شود. نیتروژن موجود در آمونیاک عنصری حیاتی برای رشد گیاهان است و استفاده از کودهای آمونیاکی باعث افزایش قابل توجهی در عملکرد محصولات کشاورزی می شود.
- صنایع برودتی : آمونیاک به عنوان یک مبرد طبیعی به دلیل راندمان بالا قیمت مناسب و سازگاری با محیط زیست به طور گسترده ای در سیستم های برودتی صنعتی و تجاری مورد استفاده قرار می گیرد. سردخانه های بزرگ کارخانجات فرآوری مواد غذایی صنایع پتروشیمی پالایشگاه ها و سیستم های تهویه مطبوع صنعتی از جمله مهم ترین کاربردهای آمونیاک در صنایع برودتی هستند.
- صنایع شیمیایی : آمونیاک به عنوان یک ماده اولیه کلیدی در صنایع شیمیایی برای تولید مواد مختلفی از جمله اسید نیتریک سودا اش الیاف مصنوعی (نایلون و اکریلیک) داروها و مواد منفجره استفاده می شود.
- صنایع پتروشیمی و پالایشگاهی : آمونیاک در صنایع پتروشیمی و پالایشگاهی برای خنثی سازی اسیدهاکنترل pHتصفیه گازهای خروجی و تولید مواد افزودنی مورد استفاده قرار می گیرد. همچنین آمونیاک در فرآیند حذف اکسیدهای نیتروژن (DeNOx) از گازهای خروجی نیروگاه ها و واحدهای صنعتی کاربرد دارد.
- صنایع داروسازی : آمونیاک در صنایع داروسازی به عنوان ماده اولیه در تولید برخی داروها و همچنین به عنوان عامل تنظیم pH در فرآیندهای تولید دارو مورد استفاده قرار می گیرد.
- صنایع معدنی و فلزی : آمونیاک در صنایع معدنی و فلزی برای استخراج فلزات از سنگ معدن تصفیه فلزات و کنترل pH در فرآیندهای متالورژیکی کاربرد دارد.
مثال هایی از صنایع مختلف :
- صنایع غذایی : سردخانه های نگهداری مواد غذایی منجمد و تازه خطوط تولید بستنی کارخانجات فرآوری گوشت و مرغ کارخانجات لبنیات کارخانجات نوشیدنی.
- صنایع پتروشیمی : واحدهای تولید آمونیاک واحدهای تولید اوره واحدهای تولید اسید نیتریک پالایشگاه های نفت و گاز.
- صنایع داروسازی : کارخانجات تولید داروهای تزریقی کارخانجات تولید آنتی بیوتیک ها کارخانجات تولید داروهای ضدالتهاب.
- صنایع کشاورزی : واحدهای تولید کودهای شیمیایی مزارع بزرگ کشت محصولات کشاورزی.
استانداردهای بین المللی و مقررات ایمنی مرتبط با آمونیاک
کار با آمونیاک به دلیل ماهیت خطرناک آن مستلزم رعایت دقیق استانداردهای بین المللی و مقررات ایمنی است. این استانداردها و مقررات با هدف کاهش خطرات ناشی از نشت آمونیاک آتش سوزی انفجار و تماس با انسان و محیط زیست تدوین شده اند. برخی از مهم ترین استانداردها و مقررات مرتبط با آمونیاک عبارتند از :
- استاندارد OSHA ۲۹ CFR ۱۹۱۰.۱۱۹ (Process Safety Management of Highly Hazardous Chemicals) : این استاندارد از سوی سازمان ایمنی و بهداشت شغلی ایالات متحده آمریکا (OSHA) تدوین شده و الزامات سیستم مدیریت ایمنی فرآیند (PSM) را برای مواد شیمیایی بسیار خطرناک از جمله آمونیاک تعیین می کند. PSM شامل ۱۴ عنصر کلیدی مانند تحلیل خطر فرآیند (PHA) رویه های عملیاتی آموزش کارکنان بازرسی و نگهداری مدیریت تغییر و برنامه ریزی واکنش اضطراری است.
- استاندارد ANSI/IIAR ۲ (Safe Design for Installations Using Closed-Circuit Ammonia Refrigeration Systems) : این استاندارد از سوی موسسه بین المللی تبرید آمونیاک (IIAR) تدوین شده و الزامات طراحی ایمن سیستم های برودتی آمونیاکی مدار بسته را ارائه می دهد. IIAR ۲ به موضوعاتی مانند طراحی سیستم انتخاب تجهیزات نصب بهره برداری نگهداری و تعمیرات سیستم های برودتی آمونیاکی می پردازد.
- استاندارد ISO ۵۱۴۹ (Refrigerating systems and heat pumps – Safety and environmental requirements) : این استاندارد بین المللی از سوی سازمان بین المللی استانداردسازی (ISO) تدوین شده و الزامات ایمنی و زیست محیطی سیستم های تبرید و پمپ های حرارتی را تعیین می کند. ISO ۵۱۴۹ به مبردها طراحی سیستم نصب بهره برداری نگهداری و بازیافت مبردها می پردازد و آمونیاک را نیز در بر می گیرد.
- استانداردهای حمل ونقل آمونیاک : حمل ونقل آمونیاک نیز تحت مقررات و استانداردهای خاصی انجام می شود. مقررات حمل ونقل مواد خطرناک سازمان ملل متحد (UN Recommendations on the Transport of Dangerous Goods)توافقنامه اروپایی حمل ونقل بین المللی جاده ای کالاهای خطرناک (ADR)کد بین المللی دریایی کالاهای خطرناک (IMDG Code) و مقررات حمل ونقل هوایی کالاهای خطرناک (IATA Dangerous Goods Regulations) از جمله مهم ترین مقررات حمل ونقل آمونیاک در سطح بین المللی هستند. این مقررات شامل الزامات بسته بندی برچسب زنی علامت گذاری مستندسازی آموزش رانندگان و پرسنل حمل ونقل و تجهیزات ایمنی وسایل نقلیه حمل ونقل آمونیاک می باشد.
فناوری های پیشرفته مرتبط با ایمنی آمونیاک :
- سیستم های تشخیص نشت گاز آمونیاک : فناوری های پیشرفته تشخیص نشت گاز آمونیاک شامل سنسورهای الکتروشیمیایی سنسورهای مادون قرمز و سیستم های تصویربرداری گاز می باشد. این سیستم ها قادرند نشت های کوچک آمونیاک را در مراحل اولیه تشخیص داده و هشدارهای لازم را به پرسنل ایمنی ارسال کنند. سیستم های تشخیص نشت گاز مبتنی بر هوش مصنوعی (AI) نیز در حال توسعه هستند که می توانند با تحلیل داده های سنسورها و الگوهای نشت دقت و سرعت تشخیص نشت را افزایش دهند.
- مواد مقاوم به خوردگی : استفاده از مواد مقاوم به خوردگی در ساخت تجهیزات آمونیاکی (مانند فولادهای ضدزنگ آلیاژهای نیکل و پلیمرهای فلورینه) می تواند عمر مفید تجهیزات را افزایش داده و خطر نشت ناشی از خوردگی را کاهش دهد. پوشش های محافظتی و بازدارنده های خوردگی نیز برای افزایش مقاومت به خوردگی تجهیزات آمونیاکی مورد استفاده قرار می گیرند.
- سیستم های مانیتورینگ و کنترل از راه دور : سیستم های مانیتورینگ و کنترل از راه دور با استفاده از اینترنت اشیاء (IoT) و شبکه های بی سیم امکان پایش مستمر وضعیت سیستم های آمونیاکی (فشار دما سطح مایع غلظت گاز آمونیاک و غیره) و کنترل از راه دور تجهیزات را فراهم می کنند. این سیستم ها می توانند در کاهش زمان پاسخگویی به حوادث و بهبود ایمنی سیستم های آمونیاکی نقش موثری ایفا کنند.
- واقعیت مجازی و واقعیت افزوده (VR/AR) : فناوری های واقعیت مجازی (VR) و واقعیت افزوده (AR) در آموزش پرسنل کار با آمونیاک و همچنین در انجام بازرسی ها و تعمیرات تجهیزات آمونیاکی کاربرد دارند. VR می تواند محیط های آموزشی شبیه سازی شده و تعاملی را برای آموزش روش های ایمن کار با آمونیاک و رویه های واکنش اضطراری فراهم کند. AR می تواند اطلاعات فنی و راهنمایی های بصری را در حین انجام بازرسی ها و تعمیرات تجهیزات آمونیاکی به تکنسین ها ارائه دهد.
چالش ها و محدودیت های فنی در کار با آمونیاک
کار با آمونیاک علیرغم مزایای فراوان با چالش ها و محدودیت های فنی متعددی همراه است که باید به دقت مورد توجه قرار گیرند :
- سمیت و خورندگی : آمونیاک یک گاز سمی و خورنده است که تماس با آن می تواند باعث تحریک شدید پوست چشم ها و سیستم تنفسی شود. استنشاق غلظت های بالای آمونیاک می تواند منجر به آسیب ریه ادم ریوی و حتی مرگ شود. آمونیاک همچنین می تواند باعث خوردگی برخی از فلزات و مواد پلیمری شود.
- قابلیت اشتعال : آمونیاک در غلظت های بالا قابل اشتعال است و مخلوط آمونیاک و هوا در محدوده غلظت ۱۵ تا ۲۸ درصد حجمی می تواند منفجر شود. اگرچه خطر انفجار آمونیاک کمتر از برخی گازهای قابل اشتعال دیگر است اما در صورت نشت مقادیر زیاد آمونیاک در محیط های بسته خطر انفجار وجود دارد.
- مدیریت فشار و دما : آمونیاک مایع در دماهای پایین و فشارهای بالا نگهداری می شود. مدیریت دقیق فشار و دما در سیستم های آمونیاکی برای جلوگیری از تبخیر بیش از حد افزایش فشار ناگهانی و نشت آمونیاک ضروری است. تغییرات دما و فشار می تواند بر عملکرد سیستم های برودتی آمونیاکی نیز تاثیر بگذارد.
- نگهداری و تعمیرات : سیستم های آمونیاکی به دلیل ماهیت خورنده آمونیاک و فشارهای کاری بالا نیاز به نگهداری و تعمیرات منظم و دقیق دارند. بازرسی های دوره ای تست های غیرمخرب تعویض قطعات فرسوده و کالیبراسیون تجهیزات ایمنی از جمله اقدامات نگهداری و تعمیرات ضروری در سیستم های آمونیاکی هستند.
- محدودیت های کاربرد در برخی صنایع : به دلیل سمیت و قابلیت اشتعال آمونیاک استفاده از آن در برخی صنایع و کاربردها (مانند سیستم های تهویه مطبوع مسکونی و خودرویی) محدود است. در این موارد مبردهای مصنوعی با ایمنی بیشتر و خواص مناسب تر جایگزین آمونیاک شده اند.
- مسائل زیست محیطی : نشت آمونیاک به محیط زیست می تواند باعث آلودگی خاک و آب های سطحی و زیرزمینی شود. آمونیاک همچنین یک گاز گلخانه ای قوی تر از دی اکسید کربن است و انتشار آن به جو می تواند به گرمایش جهانی کمک کند. با این حال باید توجه داشت که پتانسیل گرمایش جهانی (GWP) آمونیاک نسبت به بسیاری از مبردهای مصنوعی بسیار کمتر است و آمونیاک به عنوان یک مبرد طبیعی از نظر زیست محیطی نسبت به بسیاری از مبردهای مصنوعی ارجحیت دارد.
نکات کلیدی برای بهینه سازی ایمنی و بهبود عملکرد سیستم های آمونیاکی
بهینه سازی ایمنی و بهبود عملکرد سیستم های آمونیاکی مستلزم توجه به نکات کلیدی زیر است :
- طراحی ایمن سیستم : طراحی سیستم های آمونیاکی باید مطابق با استانداردهای بین المللی و با در نظر گرفتن تمامی جنبه های ایمنی انجام شود. انتخاب تجهیزات مناسب جانمایی صحیح اجزا استفاده از مواد مقاوم به خوردگی نصب سیستم های ایمنی و در نظر گرفتن سناریوهای اضطراری از جمله نکات مهم در طراحی ایمن سیستم های آمونیاکی هستند.
- آموزش و صلاحیت پرسنل : پرسنل کار با آمونیاک باید آموزش های تخصصی و کاملی در زمینه خواص آمونیاک خطرات آن روش های ایمن کار رویه های اضطراری و استفاده از تجهیزات ایمنی دریافت کنند. صلاحیت پرسنل باید به طور دوره ای ارزیابی و به روزرسانی شود.
- رویه های عملیاتی ایمن : تدوین و اجرای رویه های عملیاتی ایمن برای تمامی مراحل کار با آمونیاک (شامل راه اندازی بهره برداری خاموش کردن نگهداری و تعمیرات) ضروری است. این رویه ها باید به طور واضح و دقیق نوشته شده و به طور منظم بازنگری و به روزرسانی شوند.
- بازرسی و نگهداری پیشگیرانه : انجام بازرسی های دوره ای و نگهداری پیشگیرانه از سیستم های آمونیاکی برای شناسایی و رفع مشکلات احتمالی قبل از بروز حادثه بسیار مهم است. بازرسی ها باید شامل بررسی وضعیت تجهیزات تست عملکرد سیستم های ایمنی آزمایش های غیرمخرب و کالیبراسیون ابزار دقیق باشد.
- برنامه ریزی واکنش اضطراری : تدوین و اجرای برنامه ریزی واکنش اضطراری برای مقابله با حوادث احتمالی (مانند نشت آمونیاک آتش سوزی و انفجار) ضروری است. این برنامه باید شامل رویه های تخلیه کمک های اولیه اطفاء حریق کنترل نشت و ارتباط با سازمان های امدادی باشد. مانورهای دوره ای برای تمرین رویه های واکنش اضطراری باید به طور منظم انجام شود.
- استفاده از تجهیزات ایمنی مناسب : پرسنل کار با آمونیاک باید از تجهیزات ایمنی فردی (PPE) مناسب مانند ماسک تنفسیعینک ایمنیدستکش های مقاوم در برابر مواد شیمیایی و لباس های محافظ استفاده کنند. همچنین محیط کار باید مجهز به تجهیزات ایمنی جمعی مانند سیستم های تهویهدوش های ایمنیچشم شوی ها و سیستم های اعلام و اطفاء حریق باشد.
- ارزیابی خطر و مدیریت ریسک : انجام ارزیابی خطر و مدیریت ریسک به طور منظم برای شناسایی خطرات احتمالی ارزیابی ریسک های مرتبط و اجرای اقدامات کنترلی مناسب ضروری است. روش های ارزیابی خطر مانند HAZOP (Hazard and Operability Study) و LOPA (Layer of Protection Analysis) می توانند برای شناسایی خطرات و ارزیابی کفایت لایه های حفاظتی سیستم های آمونیاکی مورد استفاده قرار گیرند.
نتیجه گیری
کار با آمونیاک با وجود خطرات بالقوه در صورت رعایت دقیق اصول ایمنی استانداردها و به کارگیری فناوری های پیشرفته قابل انجام است. درک عمیق اصول عملکرد فنی اجزای سیستم های آمونیاکی اجرای رویه های عملیاتی ایمن آموزش و صلاحیت پرسنل بازرسی و نگهداری پیشگیرانه برنامه ریزی واکنش اضطراری و استفاده از تجهیزات ایمنی مناسب کلید ایمنی و کارایی سیستم های آمونیاکی در صنایع مختلف است. با توجه به مزایای زیست محیطی آمونیاک به عنوان یک مبرد طبیعی استفاده از آن در سیستم های برودتی صنعتی و تجاری با رعایت ملاحظات ایمنی می تواند به عنوان یک راهکار پایدار و کارآمد در راستای کاهش اثرات زیست محیطی صنایع محسوب شود. توسعه فناوری های نوین در زمینه تشخیص نشت آمونیاک مواد مقاوم به خوردگی سیستم های مانیتورینگ از راه دور و واقعیت مجازی/افزوده نقش مهمی در بهبود ایمنی و عملکرد سیستم های آمونیاکی در آینده ایفا خواهد کرد.
پرسش و پاسخ های متداول
پرسش ۱ : در صورت نشت آمونیاک چه اقداماتی باید انجام داد؟
پاسخ : در صورت نشت آمونیاک اولین اقدام تخلیه فوری منطقه آلوده و اطلاع رسانی به پرسنل ایمنی و امدادی است. از نزدیک شدن به محل نشت بدون تجهیزات ایمنی خودداری کنید. در صورت امکان منبع نشت را از راه دور قطع کنید. از ایجاد جرقه یا آتش در نزدیکی محل نشت خودداری کنید. در صورت تماس آمونیاک با پوست یا چشم محل تماس را با آب فراوان به مدت حداقل ۱۵ دقیقه شستشو دهید و به پزشک مراجعه کنید. در صورت استنشاق آمونیاک فرد مصدوم را به هوای تازه منتقل کرده و در صورت لزوم اکسیژن درمانی انجام دهید.
پرسش ۲ : آیا آمونیاک قابل اشتعال است و خطر انفجار دارد؟
پاسخ : بله آمونیاک در غلظت های بالا قابل اشتعال است و مخلوط آمونیاک و هوا در محدوده غلظت ۱۵ تا ۲۸ درصد حجمی می تواند منفجر شود. با این حال خطر انفجار آمونیاک نسبت به برخی گازهای قابل اشتعال دیگر کمتر است. برای کاهش خطر اشتعال و انفجار باید از تجمع آمونیاک در محیط های بسته جلوگیری شود از ایجاد منابع اشتعال در نزدیکی تجهیزات آمونیاکی خودداری شود و از سیستم های تهویه مناسب استفاده گردد.
پرسش ۳ : چه تجهیزات ایمنی فردی (PPE) برای کار با آمونیاک ضروری است؟
پاسخ : تجهیزات ایمنی فردی (PPE) ضروری برای کار با آمونیاک شامل موارد زیر است :
- ماسک تنفسی : ماسک تنفسی با فیلتر مناسب برای حفاظت از سیستم تنفسی در برابر استنشاق آمونیاک. نوع فیلتر باید بر اساس غلظت آمونیاک و شرایط محیط کار انتخاب شود.
- عینک ایمنی یا محافظ صورت : برای حفاظت از چشم ها در برابر تماس با آمونیاک و بخارات آن.
- دستکش های مقاوم در برابر مواد شیمیایی : دستکش های ساخته شده از موادی مانند نئوپرن یا بوتیل رابر برای حفاظت از پوست دست ها در برابر تماس با آمونیاک.
- لباس های محافظ : لباس های محافظ یکسره یا دوتکه ساخته شده از مواد مقاوم در برابر مواد شیمیایی برای حفاظت از کل بدن در برابر تماس با آمونیاک.
- کفش های ایمنی : کفش های ایمنی با پنجه فولادی و زیره مقاوم در برابر مواد شیمیایی برای حفاظت از پاها.
علاوه بر PPE استفاده از تجهیزات ایمنی جمعی مانند سیستم های تهویه دوش های ایمنی و چشم شوی ها نیز در محیط کار با آمونیاک ضروری است.
ما تو کارخونه مون چند ساله با آمونیاک کار می کنیم ولی همیشه دغدغه نشت گاز رو داریم. واقعاً سیستم های تشخیص نشتی که تو مقاله گفتین انقدر دقیقن؟ کسی تجربه استفاده داره؟
این استانداردهای بین المللی که گفتین خیلی خوبه ولی تو ایران واقعاً کسی به اینا اهمیت می ده؟ بازرسی درستی هم هست که مطمئن شیم کارخونه ها رعایت می کنن؟
مقاله خیلی کاملی بود. مخصوصاً بخش مربوط به تجهیزات ایمنی فردی. ما همیشه مشکل انتخاب ماسک تنفسی مناسب رو داشتیم. اگه میشه یه لیست از مدل های خوب و معتبر رو هم اضافه کنید.
من یه بار تو یه کارخونه بودم بوی آمونیاک خیلی شدید بود. مسئول ایمنی شون می گفت عادیه! یعنی واقعاً بوی آمونیاک تو محیط کار طبیعیه؟ اینا جون کارگرا رو به بازی گرفتن!
ما سیستم برودتی آمونیاکی داریم راندمانش عالیه ولی نگهداریش خیلی دردسر داره. هر سری تعمیرکار میاد یه هزینه سنگین میگیره. راهکاری برای کاهش هزینه های نگهداری هست؟
این شیرهای اطمینان مخازن آمونیاک واقعاً چقدر قابل اعتمادن؟ یه بار تو یه حادثه شیر اطمینان درست کار نکرد و نزدیک بود فاجعه بشه.
تو مقاله گفته بودین آمونیاک از نظر زیست محیطی بهتر از مبردهای مصنوعیه. ولی مگه نشت آمونیاک برای محیط زیست ضرر نداره؟ تکلیف آلودگی خاک و آب چی میشه؟
آموزش پرسنل خیلی مهمه کاملاً موافقم. ولی متاسفانه تو خیلی از کارخونه ها آموزش ها فقط اسمیه. کسی واقعاً وقت نمیذاره درست آموزش بده.
این سیستم های مانیتورینگ از راه دور خیلی جالبه. ولی هزینه اش چقدره؟ آیا برای کارگاه های کوچیک هم مقرون به صرفه هست؟
ما مخزن آمونیاک مون رو تازه نصب کردیم ولی هنوز مطمئن نیستیم محل قرارگیریش ایمنه یا نه. کسی هست بتونه یه مشاوره تخصصی بده؟
این واقعیت مجازی و افزوده که گفتین برای آموزش خیلی ایده خوبیه. ولی تو ایران کسی از اینا استفاده می کنه اصلاً؟
من تو کار حمل و نقل مواد شیمیایی هستم. حمل آمونیاک خیلی مسئولیت داره. اگه میشه یه کم بیشتر در مورد نکات ایمنی حمل و نقل جاده ای آمونیاک توضیح بدین.
تو مقاله به خوردگی تجهیزات آمونیاکی اشاره کردین. چه راهکارهایی برای جلوگیری از خوردگی و افزایش طول عمر تجهیزات وجود داره؟
ما چند ساله از آمونیاک برای کود استفاده می کنیم. ولی همیشه نگرانیم که موقع استفاده خودمون یا کارگرها آسیب ببینیم. نکات ایمنی استفاده از کود آمونیاکی رو هم بگین.
این محدودیت های کاربرد آمونیاک تو صنایع خاص رو بیشتر توضیح بدین. چرا مثلاً تو سیستم های تهویه مطبوع خونگی نمیشه ازش استفاده کرد؟
من یه بار شاهد نشت آمونیاک تو یه کارخونه بودم. واقعاً صحنه ترسناکی بود. بوی خیلی بدی داشت و همه فرار می کردن. خدا رو شکر تلفات نداشت.
این تست های غیرمخرب که برای خطوط لوله آمونیاک گفتین هزینه ش خیلی بالاست. آیا واقعاً ضروریه؟ نمیشه یه تست ارزون تر جایگزین کرد؟
ما سیستم اعلام و اطفاء حریق برای مخزن آمونیاک مون نصب کردیم ولی مطمئن نیستیم در شرایط اضطراری درست کار کنه. تست دوره ای این سیستم ها چطوریه؟
این برنامه واکنش اضطراری که گفتین خیلی مهمه. ولی متاسفانه تو بیشتر کارخونه ها فقط یه برگه رو دیواره هیچ کس هم نمی دونه توش چی نوشته.
به نظر من مهم ترین نکته تو کار با آمونیاک رعایت ایمنیه. هیچ چیز مهم تر از جون آدما نیست. مقاله خوبی بود امیدوارم همه جدی بگیرنش.